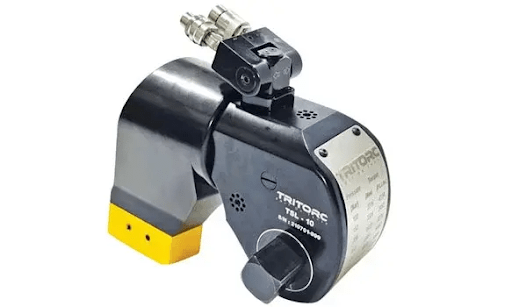
Precision and efficiency are essential to a hydraulic torque instrument. Hydraulic torque wrenches are really important tools that help ensure we tighten bolts accurately and with control in different situations. Creative manufacturers who focus on making top-notch tools and using the latest technology are behind these powerful instruments.
Hydraulic Torque Wrenches
Hydraulic torque wrenches are tools made to accurately turn bolts and nuts. They use hydraulic power to create precise turning force, and they’re essential in industries where being exact and trustworthy is crucial. Whether putting together wind turbines or keeping oil rigs in good shape, hydraulic torque wrenches ensurevital structures and machines stay solid and reliable.
Top of Form
Uses of Hydraulic Torque Wrenches
The several uses of hydraulic torque wrenches include:
Construction and Infrastructure: Hydraulic torque wrenches are extensively used in the construction and infrastructure sectors, where precision and reliability are essential. These tools are used in building structural components, ensuring that bolts are tightened to exact specifications. Hydraulic torque wrenches are essential in maintaining the structural integrity of buildings and bridges, from constructing steel structures to securing concrete elements.
Oil and Gas Industry: In the oil and gas industry, where equipment operates under extreme conditions, hydraulic torque wrenches are essential for securing flanges and connections. The torque accuracy provided by these wrenches is critical in preventing leaks and maintaining the safety and efficiency of oil rigs and pipelines. Their ability to deliver precise torque in challenging environments makes them an important element in this sector.
Power Generation: Hydraulic torque wrenches are extensively used in power generation facilities, particularly in assembling and maintaining turbines and generators. These tools ensure that the bolts securing critical components are tightened uniformly, contributing to the reliability and efficiency of power plants. The ability to achieve accurate torque levels is crucial in preventing equipment failure and downtime.
Mining Industry: The mining industry requires robust equipment to extract valuable resources. Hydraulic torque wrenches are vital in assembling and maintaining heavy machinery used in mining operations. Whether securing components in drilling equipment or maintaining crushers and conveyors, these tools contribute to the longevity and safety of mining operations.
Advantages of Hydraulic Torque Wrenches
Various advantages of hydraulic torque wrenches are:
Precision and Accuracy: One of the primary advantages of hydraulic torque wrenches is that they provide precise and accurate torque. This ensures that bolts are tightened to the required specifications, preventing under-tightening or over-tightening.
Speed and Efficiency: Hydraulic torque wrenches operate at high speeds, significantly reducing the time required for tightening bolts compared to manual methods. This speed and efficiency are particularly beneficial in industries where time is important, contributing to increased productivity and cost-effectiveness.
Safety: The hands-free operation of low-profile hydraulic wrench enhances safety in industrial settings. Operators can control the tool remotely, minimising the risk of injuries associated with manual torque application. The precise torque control also reduces the likelihood of accidents and equipment failures.
Versatility: Hydraulic torque wrenches come in various sizes and configurations, making them versatile tools for different applications. Whether in confined spaces or large-scale industrial settings, these wrenches can be adapted to meet the specific torque requirements of diverse projects.
Technological Advancements
Hydraulic torque wrench manufacturers in India are at the forefront of technological advancements, constantly innovating to meet the evolving needs of industries. Smart torque wrenches with digital controls, wireless communication capabilities, and advanced torque monitoring systems are becoming standard features. These innovations enhance precision and contribute to the overall safety and efficiency of industrial operations.